Product Features
Simdroid-EC empowers enterprises to validate thermal design concepts through simulation during early prototyping phases, significantly reduces physical testing iterations and accelerates product development cycles.
Rapid Modeling
Simdroid-EC features an extensive Flex Part Model Library with parameterized editing functions. It enables user-friendly CAD operations such as drag-and-drop, auto-snapping, and auto-alignment for streamlined workflow efficiency.
Full-Scale Thermal Simulation
Simdroid-EC enables full-scale modeling from chip level, PCB level, device level to system-level. It supports cross-scale orthogonal meshing and comprehensive thermal management scenarios, such as thermal conduction, natural convection cooling, forced air cooling, liquid cooling, thermal radiation, solar radiation, and thermoelectric cooling.
Efficient Solution Solving
Simdroid-EC has an efficient CFD solving algorithm with superior convergent capability. It can automatically compute initial field, set solution control parameters and convergence conditions, as well as compute components' fluid flow and heat transfer data.
Application Scenarios
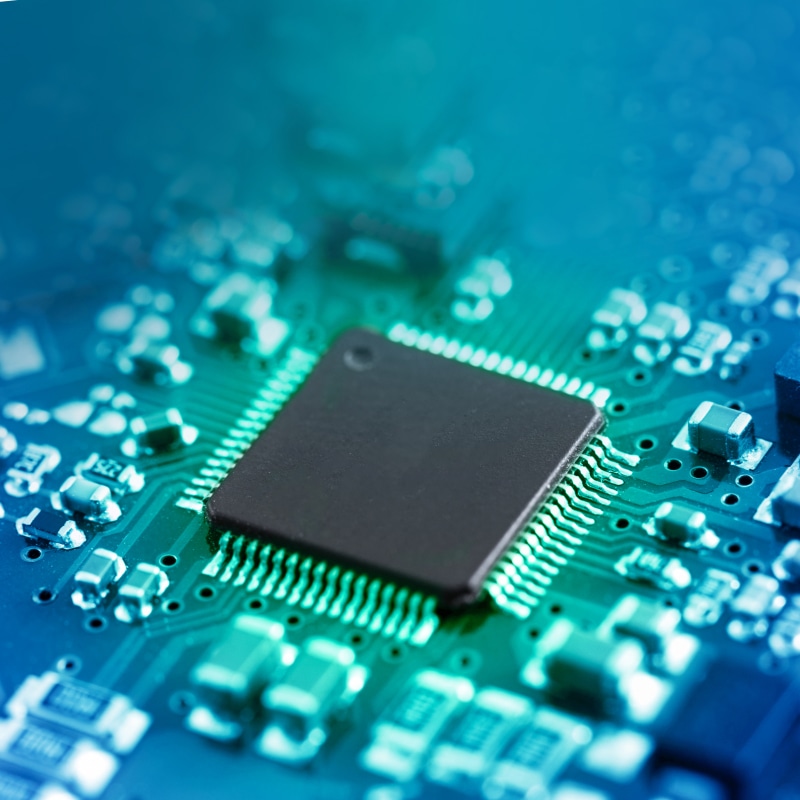
Chip & Package-Level Thermal Design and Analysis
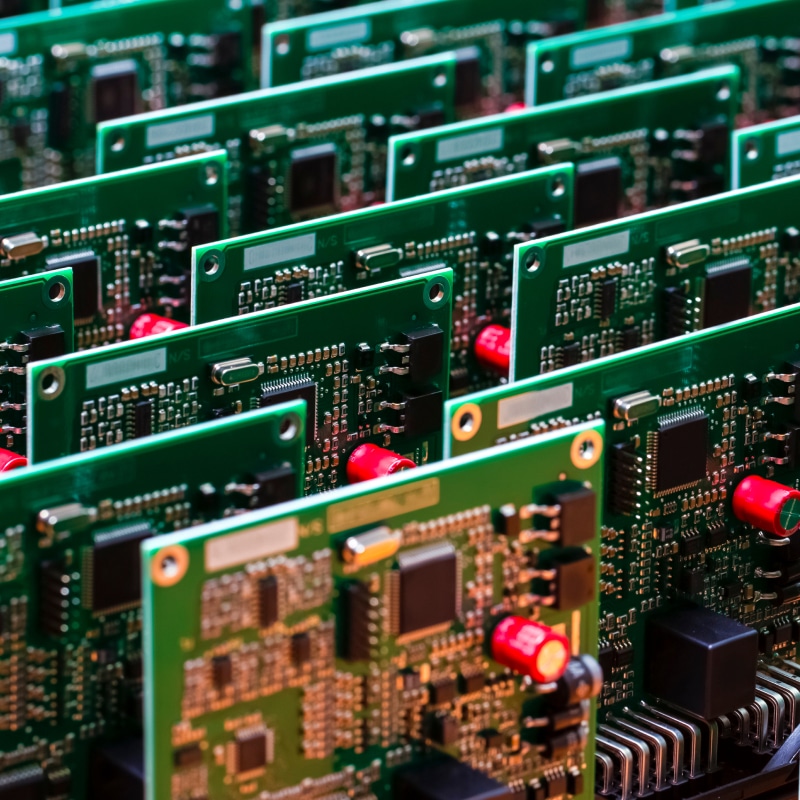
PCB & Module-Level Cooling Optimization
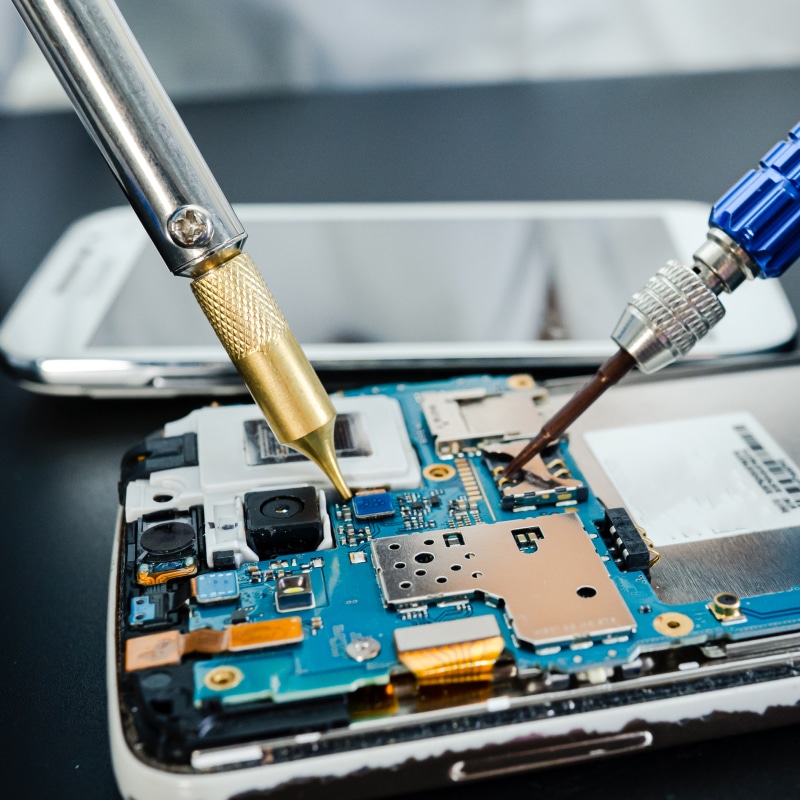
Full-Scale Thermal Simulation for Compact Devices (Mobile Phones, Tablet PC, Chassis and Cabinets)
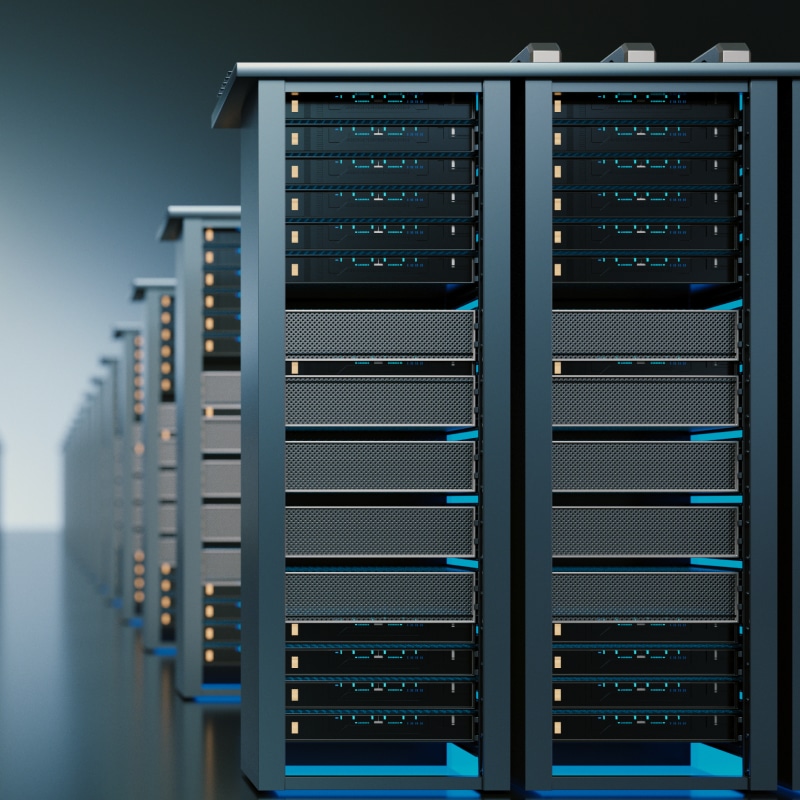
System-Level Ventilation and Thermal Management (Server Rooms and Data Centers)
Core Functions
Rapid Modeling
Meshing
Solution Method
Postprocessing