SimRelia Reliability Analysis Platform is a dedicated "Simulation + Reliability Analysis" engineering module developed by IBE in collaboration with the Reliability Engineering Institute of Beihang University. It integrates engineering probability algorithms and reliability mechanism models in the field of reliability analysis into the IBE general simulation PaaS platform Simdroid to create an autonomous and controllable solution.
With an integrated digital environment, SimRelia supports integrated design and simulation analysis, which can evaluate unit reliability and system reliability of components, equipment, subsystems, and systems while considering various sources of uncertainty. This helps address safety design issues in complex engineering structures and provides solutions for uncertainty description, reliability analysis, sensitivity analysis, and uncertainty-based structural optimization design.
- Unit reliability analysis includes uncertainty analysis and reliability analysis. Uncertainty analysis is to perform uncertainties analysis in geometric parameters, material properties, operating loads, and other uncertain factors for the unit. Reliability analysis is to conduct finite element iterative analysis on units based on the sample space generated by uncertainty analysis to obtain the sample space of simulation response variables. On this basis, failure mechanism models are invoked for reliability analysis to obtain reliability and fatigue life under different failure mechanism models.
- System reliability is evaluated by invoking system reliability model based on the reliability of individual components and the integrated various system reliability analysis models such as Fault Tree Analysis (FTA) and Reliability Block Diagram (RBD).
- SimRelia integrates robust reliability algorithms and uses Simdroid's encapsulation features to create a series of reliability analysis apps, quickly achieving reliability assessments for components and systems.
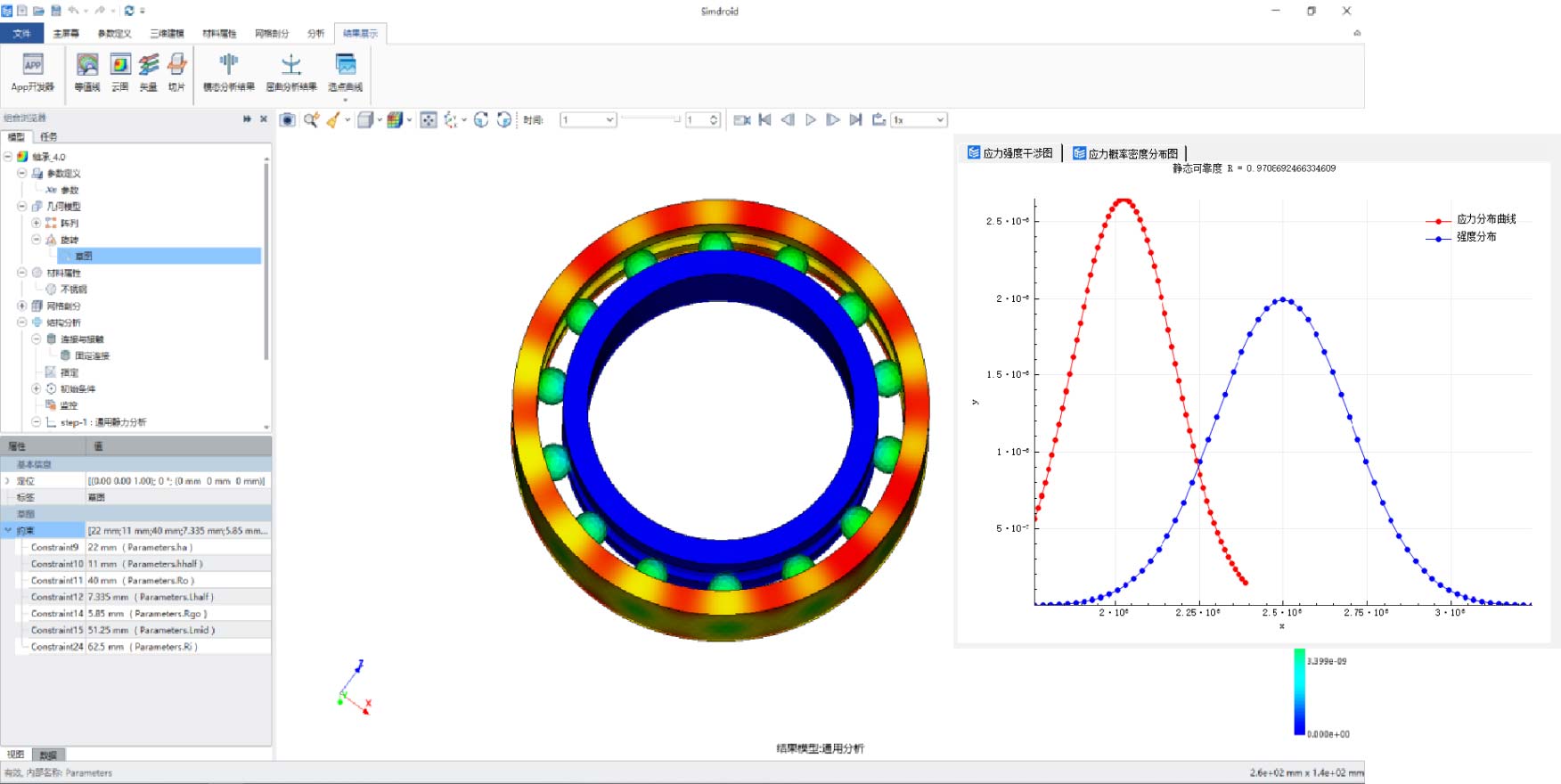
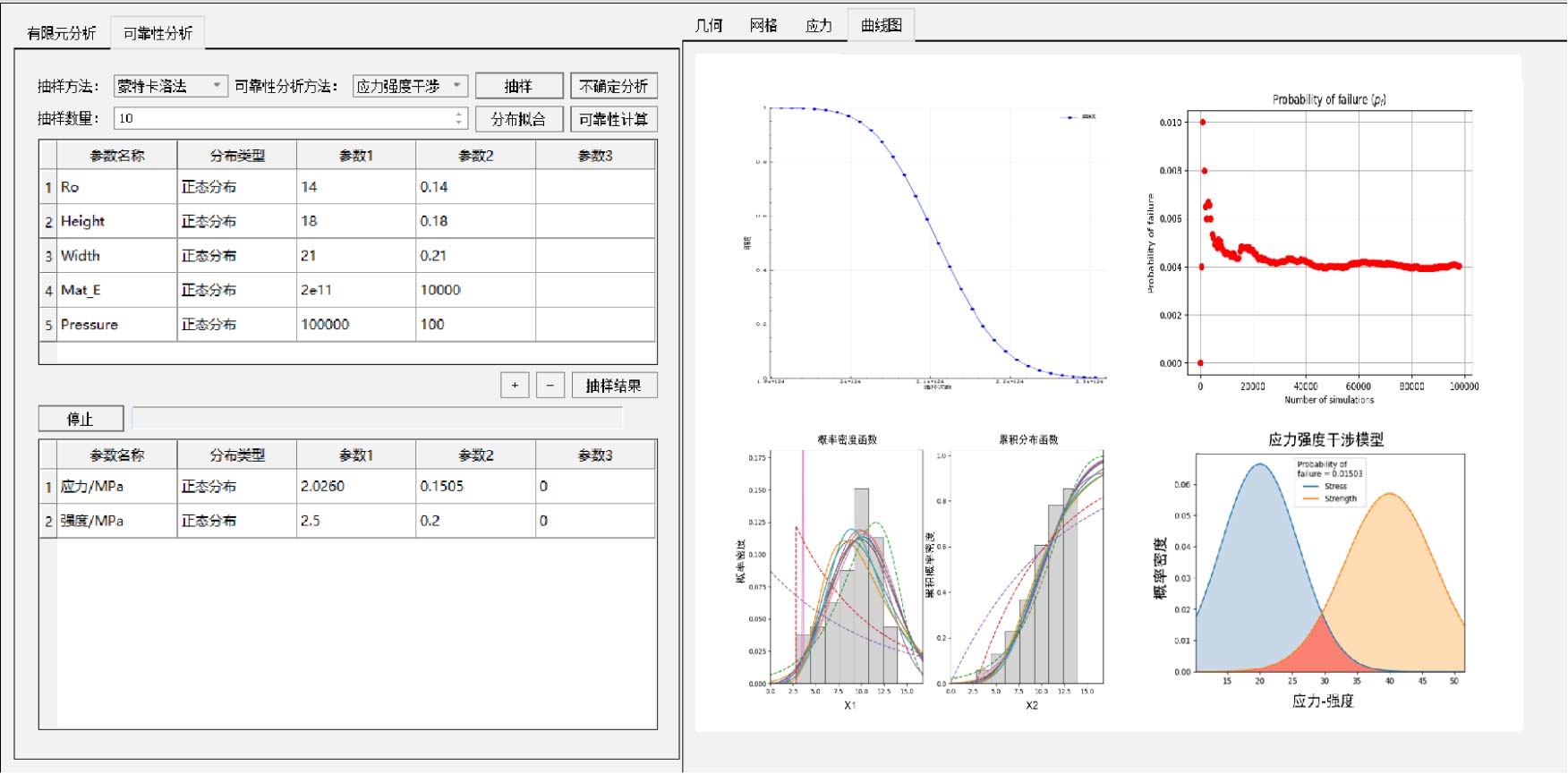
In order to meet the requirements of a research institute for design knowledge solidification and collaborative simulation, IBE customized and developed a simulation cloud platform system of "Simulation Platform + Simulation Apps". The platform contains algorithm layer, platform layer, and application layer, corresponding to the underline solver algorithm, visual simulation development environment, simulation app design, and execution environment. It encapsulates and solidifies hundreds of aero-engine industrial simulation apps, which can be widely used in aero-engine R&D, purchasing and supply, production and manufacturing, operation and management, enterprise management, and product lifecycle management, etc., and effectively improve the R&D capability and cloud-based interoperability of the research institute.
- Deploying 300 aero-engine apps on INDICS, each app corresponds to an R&D model, solidifying industrial knowledge and experience, and improving the industry's intelligent manufacturing level through scalable reuse.
- Free researchers and developers from the boring and repetitive labor works.
- Lower the simulation threshold to enable engineers to use the app quickly and repeatedly.
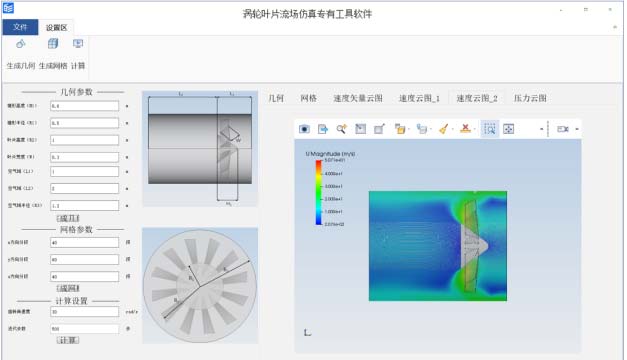
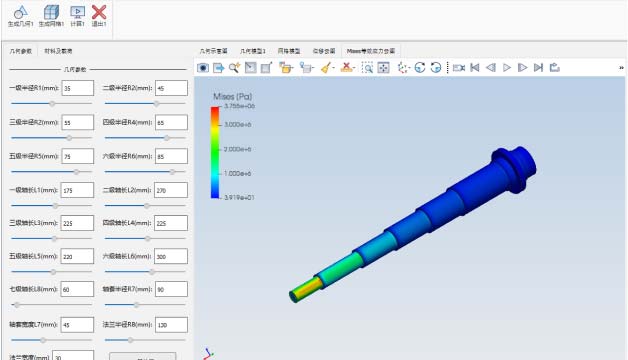
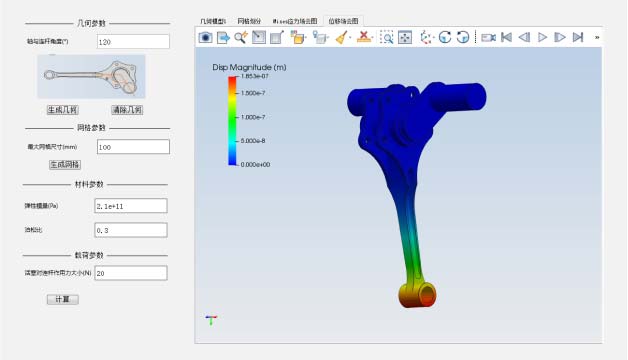
Power transmission is a crucial component of the electrical industry, requiring the construction of transmission line towers in various complex terrain conditions. In this context, brackets are essential installation equipment during tower construction, whose safety and reliability are of utmost importance during the construction process.
Considering the characteristics of the actual application scenario of the bracket, IBE's simulation consulting team comprehensively addressed the safety assessment needs of brackets under the design and construction phases, and developed a user-friendly and accurate safety assessment app for bracket construction processes based on the general simulation PaaS platform Simdroid. It allows for rapid modeling and precise stress analysis of brackets. Code-free encapsulation and cloud deployment of apps not only meet the demand for quick parameterized simulations in variable scenarios but also break the spatial and temporal constraints of simulation collaboration, providing effective solutions for engineering problems consulted by customers.
- It allows for the rapid modeling of brackets, and can carry out parametric modeling and calculation of bracket cross-sections, equal-angle steel sections, bracket materials, cable parameters, and operating conditions. Through rich visualization post-processing techniques, it enables precise and reliable analysis of the bracket's structural behavior.
- By inputting data based on the actual on-site conditions, it can quickly obtain calculation results, obtaining the accurate stress situation of the bracket system, which facilitates adjustments to hazardous conditions and ensures safe tower assembly during construction.
- The rapid simulation analysis under variable structural and operating conditions driven with intuitive parameters significantly reduces the threshold for using simulation technology, which can provide effective support for solving practical engineering problems.
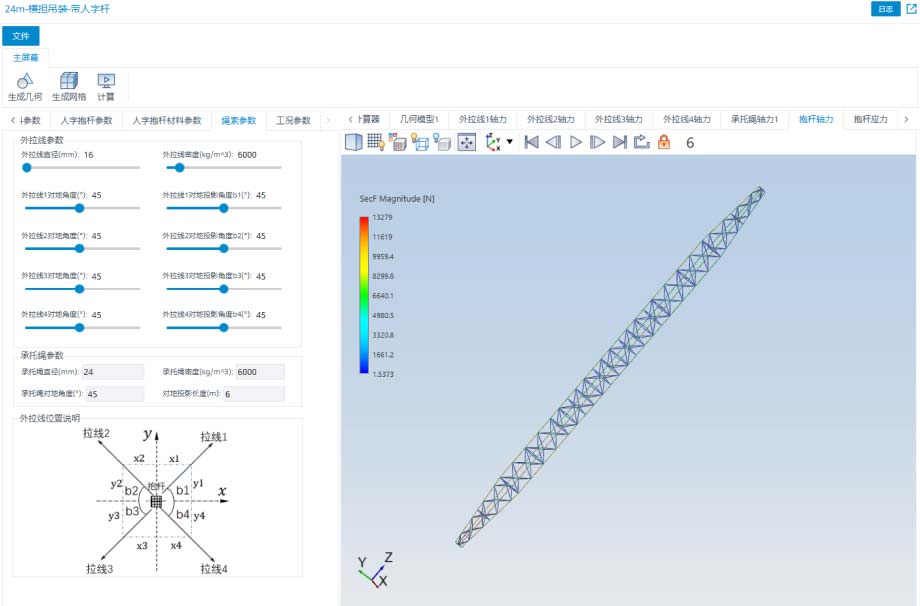
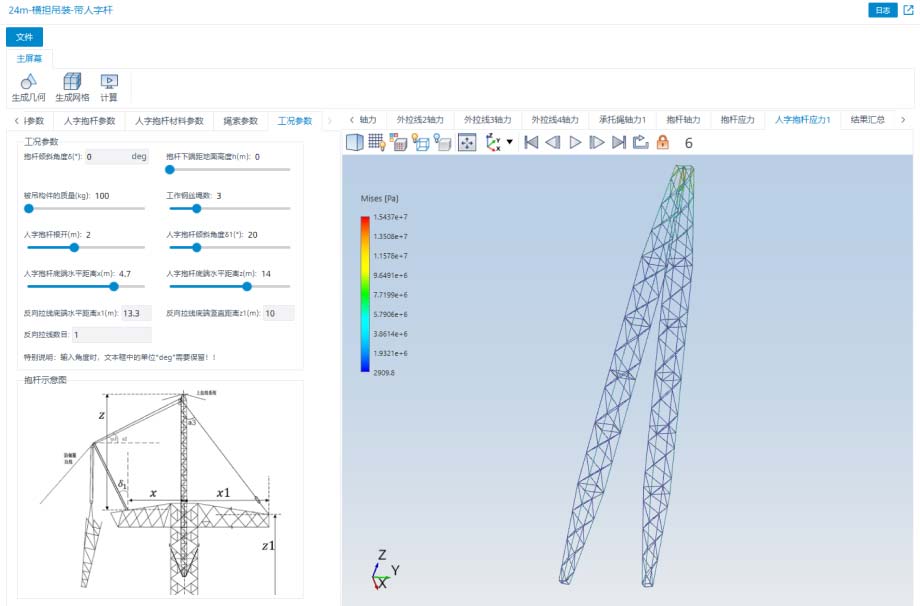